2. Description of the business of the synthos sa group
The business of the Group is divided into four main segments: butadiene and rubber (“Synthetic Rubber Segment”), styrene and its derivatives (“Styrene Plastics Segment”), dispersions, adhesives and latex (“Dispersions, Adhesives and Latexes Segment”), and plant protection chemicals (AGRO). The last of these segments has been split off in 2015. The Group also derives revenues from ancillary activities related to production and distribution of heat from its own power plants and revenues from electricity trading and distribution (“Other Operations”, including “Utilities” which are presented as a separate segment in the consolidated financial statements). Other Operations comprise also revenues and expenses not allocated to other segments.
The business of the Group relies on three main segments:
Synthetic Rubber Segment
The Synthetic Rubber Segment is a core segment of the Group’s business. The Group’s offtakers of roughly 80% of the sales volume of the products in this segment are the principal tire market players, including Michelin, Continental, Bridgestone, Goodyear and Pirelli. The remaining 20% of sales volume in this segment is split among various other markets, including manufacturers of technical rubber goods, soles of footwear, elastic cables and transmission belts. In 2016 the Synthetic Rubber Segment generated sales revenues totaling PLN 2,146 million and EBITDA of PLN 363 million for the 12 months ending on 31 December 2016.
Synthetic rubbers sales volume dynamics (2008 = 100)
Styrene Plastics Segment
The Styrene Plastics Segment manufactures three main types of products with varying purposes. The first is expandable polystyrene (EPS), used mainly to produce thermal insulation boards, a basic material used for thermal insulation in the Central European construction industry. The second type includes general purpose polystyrene (GPPS) and high impact polystyrene („HIPS”), used mainly in the food packaging industry. Polystyrene is used to manufacture disposable tableware, cups, packaging for dairy products, trays and cutlery. It is also used as the basic material to produce shower cabins, jewelry packaging and in other applications where the final product must be stiff, yet transparent. The third group comprises boards from extruded polystyrene (XPS). XPS is mainly used in the construction industry for thermal insulation of buildings, reverse layer roofs, floors, thermal bridges and cavity walls.
Styrenics sales volume dynamics (2008 = 100)
In the 12 months ending on 31 December 2016, the Styrene Plastics Segment generated sales revenues totaling PLN 2,111 million and EBITDA of PLN 226 million.
Dispersions, Adhesives and Latexes Segment
The Dispersions, Adhesives and Latexes Segment produces three groups of products. The first are acrylic, styrene-acrylic and vinyl dispersions. Their main application is the manufacturing of paints, acrylic plasters, primers, sealants and many other chemicals used in the construction industry, as well as adhesives for wood and the paper industry. The second group consists of adhesives intended mainly for the wood, furniture and paper industries. The third group includes butadiene and styrene latexes used mainly to produce foam products and carpets. In the 12 months ending on 31 December 2016, the Dispersions, Adhesives and Latexes Segment generated sales revenues totaling PLN 195 million and EBITDA equal to PLN 29 million.
Dispersions&Adhesives&Latex sales volume dynamics (2008 = 100)
Agro Segment
The segment’s domain is to produce and sell plant protection means, seed dressing agents, biocidal products and leaf fertilizers. Products representing each category provide protection to crops from sowing to harvesting, defending the plants against the destructive effects of pathogenic fungi, pests and weeds and providing them with the necessary microelements and macroelements in the form of specialist fertilizers. In addition to the production of pesticides, the Agro Segment also offers services to domestic and foreign customers in the field of formulation and packaging of liquid and slurry plant protection products. In the 12 months ending on 31 December 2016, the Agro Segment generated sales revenues totaling PLN 81 million and EBITDA of PLN 3 million.
Utilities Segment
This segment deals with generation and distribution of heat, generation of electricity in combined heat and power units and distribution of electricity. In the 12 months ending on 31 December 2016, the Utilities Segment generated sales revenues totaling PLN 206 million and EBITDA of PLN 99 million.
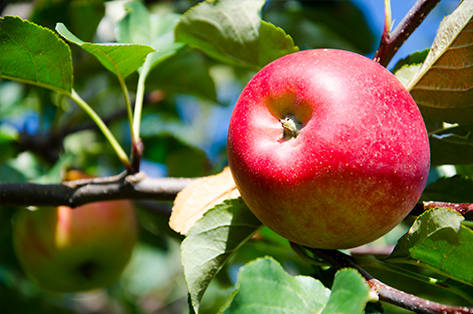
In 2014, the Group decided to launch operations in a new segment, namely the manufacture of plant protection means.
Synthos S.A. was founded in 1945 as the Synthetic Fuel Factory in Oświęcim. In the 1950s and 1960s, the construction of a synthetic rubber manufacturing plant was completed, and in June 1959, production of emulsion synthetic rubber started. The factory continued to develop, reaching maximum productivity and high employment levels in the 1970s. In 1996, it was turned into a private company, with 60% of stock transferred to the National Investment Fund.
The company was listed on the WSE in December 2004, and in 2006 the controlling interest held by majority stockholder Michał Sołowow exceeded 50%. In July 2007, the Company purchased 100% of shares of the Czech company Kaucuk a.s., one of the Group’s largest competitors in Central and Eastern Europe. In 2007, the Company signed a license agreement with Michelin for neodymium butadiene rubber (NdBR) technology used to produce polybutadiene rubbers, as well as a trade agreement to ensure deliveries of the output.
The company owns 49% of the joint venture and has a share in the operational management of the plant whose manufacturing capacity is 130,000 tons of rubber per year. In the third quarter of 2011, the Kralupy plant started to produce NdBR polybutadiene rubbers. In March 2012, the Group’s stock was included in the WIG20 (blue chip) index on the WSE.
In 2014, the Group decided to launch operations in a new segment, namely the manufacture of plant protection means. In 2014 the Company acquired a 100% equity stake in Zakład Doświadczalny „Organika” Spółka z ograniczoną odpowiedzialnością and took over the registration of plant protection products and biocidal products from Zakłady Chemiczne Organika-Azot S.A. The Group’s penetration of the market with a new offering of plant protection products will allow it to prepare customers for a product portfolio that is much wider and larger in scale, and which the Group intends to offer once the construction of its own complex of installations to produce active substances and plant protection means is completed.
In August 2015, the Group launched a new production plant in Oświęcim to manufacture modern solution styrene-butadiene rubbers (SSBR). Manufacturing will be based on a license from The Goodyear Tire & Rubber Company.
a) Acquisition of the EPS (Expandable Polystyrene) business from the INEOS Group.
On 6 May 2016, Synthos S.A. entered into an agreement with INEOS Industries Holdings Limited seated in Lyndhurst, United Kingdom, to purchase the INEOS Group’s EPS business. The total purchase price for this business was EUR 80 million, subject to possible adjustments following from the agreement.
Under the INEOS Styrenics purchase transaction Synthos S.A. acquired, among others, 3 production facilities, 2 of which are located in northern France (Wingles and Ribécourt) and the third one in the Netherlands (Breda).
In addition, Breda has a modern technological center, comprising a specialized research laboratory and pilot facilities testing innovative products marketed by the company.
The purchase of INEOS Styrenics will enable Synthos S.A. to deliver top quality expandable polystyrene (EPS) and maintain the leading position of styrofoam products among insulation materials.
The Synthos Group’s styrene processing capacity exceeds 600 thousand tons per annum. Obtaining competitively priced styrene will be possible in the longer run, in particular by expanding new styrene production capacity and will entail significant capital expenditures.
The Company reported the details of the transaction in Current Report no. 16/2016 dated 6 May 2016.
On 26 August 2016 the Company became aware of fulfillment of the condition precedent defined in the Share Purchase Agreement as on 26 August 2016 the European Commission granted unconditional approval to effect the transaction, i.e. transfer of the shares of INEOS Styrenics European Holding B.V. in performance of the Share Purchase Agreement, which the Company reported in Current Report no. 35/2016 of 26 August 2016.
The Company reported the performance of the transaction in Current Report no. 36/2016 of 31 August 2016.
b) Extension of the license – entering into an agreement with Michelin Group entities
On 26 August 2016, in connection with the license agreement of 05 October 2007, a memorandum of agreement was entered into by and between Compagnie Générale des Etablissements Michelin seated in Clermont-Ferrand, France; Michelin Recherche et Technique S.A. seated in Granges-Paccot, Switzerland, as the licensors, and Synthos S.A., as the licensee
The executed memorandum of agreement provides for increasing the production capacity of NdBR rubber permitted under the license to 132,000 tons per annum. The fee for extending the license consists of a flat fee and a variable component in the form of royalties depending on the sales volume of the licensed products.
c) Restart of the cracker in Litvinov on 19 October
On 19 October 2016, Unipetrol a.s. (PKN Orlen S.A.’s subsidiary) announced restart of the cracker in Litvinov, Czech Republic. The cracker in Litvinov supplies Czech entities from the Synthos Group with raw materials for production of ethylbenzene / styrene and butadiene, transported by pipelines. In connection with the failure of the cracker in August 2015 these raw materials had to be supplied by rail transport from other supply sources.
Reinstating product feed from the local cracker in Litvinov will make a positive contribution to stabilizing the production level and improving the margins commanded on styrene plastics and synthetic rubbers in subsequent reporting periods.
The major investments in the production area envisaged in the Group’s strategy pertain to raw material security and expansion of the product offering for customers.
The Group’s value growth strategy pursued by the Management Board calls for strengthening the Group’s position in key business areas, i.e. production of synthetic rubber, polystyrenes, dispersions and adhesives, and plant protection chemicals. The Company intends to attain this objective through, among other things, production and capital investments (acquisition of other companies conducting similar activity). The Group’s strategy assumes maintaining a safe level of debt during the development process.
Growing shareholder value is the strategic objective of the Company’s Management Board. Achieving this objective will be supported by maintaining stable long-term relationships with business partners, improving operating efficiency and expanding and modernizing the product portfolio.
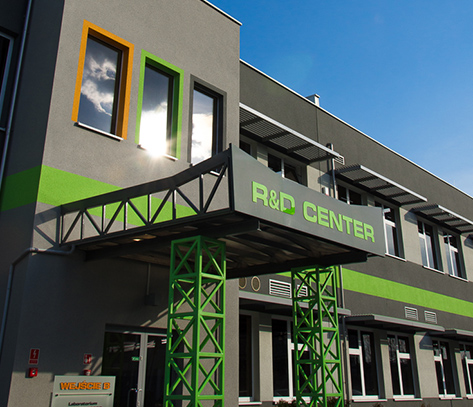
The Group assumes constant development and optimization of the product portfolio meeting customer expectations. Product development is to rely primarily on own research carried out by the Research and Development Center, whose task is to develop and implement the production of new, innovative products, primarily new types of synthetic rubber. The Group’s objective is to steadily improve its quality and cost competitiveness in relation to leading businesses in the chemical industry.
Acquisitions will focus on entities with modern products that expand the Group’s existing product portfolio and on market opportunities, i.e. relatively low-priced companies with good market prospects.
Highlights
The Synthetic Rubber Segment is the fundamental segment in the Group’s business. The segment manufactures synthetic rubber by means of emulsion polymerization of butadiene and styrene (or other chemicals such as acrylonitrile or the appropriate organic acid). In the year ended 31 December 2016, the annual manufacturing capacity as regards synthetic rubber (ESBR, NBR, HSR, NdBR) was approximately 375,000 tons. In 2015, an installation to produce SSBR rubbers was also commissioned with a production capacity of 90,000 tons per year. In the year ending 31 December 2016 the Group’s Synthetic Rubber Segment generated sales revenues of PLN 2,146 million and EBITDA of PLN 363 million.
The Group produces four different kinds of synthetic rubber: styrene butadiene rubbers, polybutadiene rubbers, high styrene rubbers and nitrile butadiene rubbers (NBR).
Main products and applications
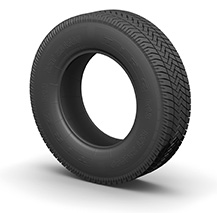
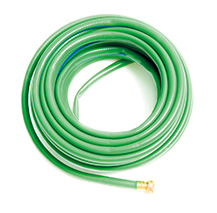
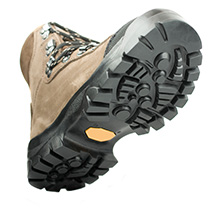
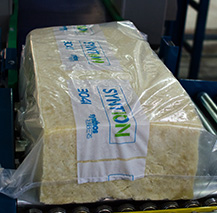
The Synthetic Rubber Segment includes the following products:
- Emulsion styrene and butadiene rubbers (EBSR) are produced in a low- temperature emulsion copolymerization process and coagulated using an acid- synthetic coagulant system. Some types of butadiene and styrene rubbers contain an admixture of aromatic Styrene butadiene rubbers are stabilized using staining or non-staining antioxdants. Styrene butadiene rubbers are used to manufacture tires, tire tubes, transmission belts, footwear, cable insulation, hoses and other technical rubber goods. Non-staining types of rubbers are used to manufacture light colored floor linings, bicycle tires and tubes, footwear, toys, cables, hoses and various other rubber goods in light pastel colors. ESBR is the most commoditized group of synthetic rubbers. Although consumed globally, demand levels are particularly high in North America, Western Europe and Northwest Asia, especially China. The majority of ESBRs is used to produce tires, but demand in other industries is also significant. The styrene butadiene rubbers produced by the Group are sold under the KER® (produced in the production facilities in Poland) and KRALEX® (in the production facilities in the Czech Republic) trademarks.
- Solution styrene butadiene rubbers (SSBR) are produced via copolymerization of butadiene and styrene in an organic solvent in the presence of a lithium catalyst. Some of them contain an admixture of naphthenic or aromatic plasticizing oil. The rubbers also vary by parameters such as Mooney’s viscosity, styrene content or vinyl structure. They are stabilized with a non-staining antioxidant. A manufacturing installation with a capacity of 90,000 tons per year has been started in August The manufacturing capacity can also be used in part to produce butadiene rubbers (LiBR). The main application for SSBR rubber (over 90% of demand) is, as with NdBR, the production of rubber mixes for treads of green high-performance tires with lowered rolling resistance. Rubber types with no oil admixtures can be used for the production of technical rubber goods, including goods in light colors. SSBRs produced in Poland are sold under the SYNTION® trademark.
- Polybutadiene rubbers (NbDR and LiBR) are obtained by means of polymerization in a solution based on a neodyme (NdBR) or lithium (LiBR) catalyst. Butadiene rubbers do not contain plasticizers and are stabilized by a non-staining antioxidant. Butadiene rubber has become the second largest type of synthetic rubber Group produces in terms of volume, after ESBR. In the year ended 31 December 2016, the Group’s annual production capacity exceeded 80,000 tons. NdBR rubbers are used mainly to produce car tires (especially treads and sidewalls), which account for about 70% of global BR consumption. Additionally, NdBR finds application in the manufacturing of technical goods, such as hoses, belts, soles of footwear, and golf balls. Thanks to its low polydispersity and glass transition temperature, it is preferred for mixes used in manufacturing of low rolling resistance tires, so called “green” tires whose use helps reduce the fuel consumption ratio. Regulations supporting the manufacturing of “green” tires, already in force in Western Europe, have significantly increased demand for NdBR. LiBR is mainly used to modify plastics, such as high impact polystyrene (HIPS). The group sells butadiene rubbers produced in the Czech (NdBR) and Polish (LiBR) plants under the SYNTECA®
- High styrene rubbers (HSR) are suitable for producing floor linings, cables, toys, rubbers for the footwear industry and hard rubber goods. The Group produces a standard grade type of high quality high styrene rubber under the KER® 1904 trademark. The rubber is obtained by mixing latexes: butadiene and styrene latexes and high styrene resin at an appropriate ratio with subsequent coagulation using a synthetic coagulant. The Group also produces the KER® 1909 high styrene rubber which a type of off-grade high styrene rubber The KER® 9000 high styrene resin is obtained via emulsion copolymerization of styrene and butadiene with subsequent coagulation using aluminum sulfate. All three types of products are stabilized using non-staining stabilizers. The high styrene rubbers and resins produced by the Group in Poland are sold under the KER®
- Nitrile (acrylonitrile-butadiene) rubbers are produced by means of cold emulsion copolymerization of butadiene and acrylonitrile and coagulated using an acid- synthetic coagulant system. Stabilized with a non-staining antioxidant. Nitrile rubbers are intended for production of technical goods resistant to the effects of oils and liquid Nitrile rubbers contain a non-staining stabilizer and thus can be used to produce goods in light colors. Nitrile rubbers produced in Poland are sold under the KER® trademark.
Customers
The Group’s major customers are car tire manufacturers as offtakers of roughly 80% of the production volume of the Synthetic Rubber Segment. The Group supplies global tire manufacturers such as Continental, Michelin, Goodyear, Bridgestone and Pirelli, delivering rubber mainly to their European manufacturing plants. The Group also supplies rubber to smaller tire manufacturers such as Nokian Tyres, Trelleborg and Apollo. Other customers include manufacturers of technical rubber goods, transmission belts, floor linings and carpets, soles of footwear and various rubber mixtures. Kralburg (Austria), Metso (Sweden), Fenner Dunlop (The Netherlands), Semperit (Austria), and in Poland: Geyer & Hosaja Mielec, Sempertrans Bełchatów owned by the Semperit Group, Stomil Sanok and Fagumit are examples. In the years ending on 31 December 2016 and 31 December 2015 the Group sold 59.0% and 60.3%, respectively, of the synthetic rubber it produced in Europe, with Asia and the two Americas accounting for the rest.
Raw materials and energy
The principal raw materials used to produce synthetic rubber are butadiene and styrene. Butadiene is produced by processing the C4 fraction in the steam cracking process. The resulting amount of butadiene depends mainly on a cracker’s feedstock, which means that the possibility of obtaining butadiene is directly proportional to the mole mass of the feedstock. The group produces butadiene from the C4 fraction in an extraction-distillation process. Most European steam crackers are currently running on heavier types of feedstock, such as naphtha or LPG, that allow to produce a stable supply of butadiene. As shale gas deposit exploration picks up pace, increasing numbers of crackers are being switched to lighter feedstock types, such as ethane, which offer a higher profit margin but also reduce the butadiene yield. This trend to switch is especially apparent in Northern American installations, which experienced a butadiene supply deficit in recent years.
Thanks to strong relationships with its largest suppliers from the petrochemical sector, the Group was able to secure long-term supply agreements for C4 fraction and butadiene. The Group also commenced to develop its own, dedicated technology to produce monomers from renewable feedstock.
In addition, the Group uses ethylene and benzene to manufacture styrene and uses it to produce its own derivatives, such as polystyrene, EPS and synthetic rubber. The Group cuts manufacturing costs thanks to relatively low labor costs, favorable feedstock supply agreements and low energy costs from an in-house combined heat and power plant. Additionally, the Group is the only manufacturer of styrene in Central and Eastern Europe, which gives it a logistical advantage over its competitors operating in Western Europe and Russia. Additionally, styrene as a raw material can be obtained in significant quantities from external sources, both from European and non-European manufacturers. Consequently, the Group can always conclude a long-term styrene supply agreement at a price dependent on the volume of purchases.
Competitors
The Group is Europe’s largest manufacturer of high quality commodity grades of emulsion synthetic rubber and the second largest manufacturer of polybutadiene rubbers with neodymium catalyst in terms of production capacity. Most articles produced by the Group have been known on the market for decades, with products sold under the KER® and KRALEX® trademarks present on the market since more than 50 years. They have recently been joined by SYNTECA® and, in 2015, SYNTION®.
The Group’s major competitors include: Arlanxeo, a German manufacturer of chemicals offering a wide range of products for the tire industry and industries offering general purpose rubber goods; followed by Versalis, one of the most important European rubber manufacturers; Trinseo, an international manufacturer of plastics, latex and rubber; and Kumho Petrochemical, an international concern producing chemicals, whose basic offering includes synthetic rubber, synthetic resins, specialty chemicals, chemicals for the electronic and energy industries, and chemicals used to produce construction materials and technologically advanced materials.
Highlights
In 2016, the Group was one of the leading manufacturers of polystyrene and expandable polystyrene in Europe. The Group’s Styrene Plastics Segment produces four main types of products obtained in styrene polymerization process and used for different areas of application: EPS, GPPS, HIPS and XPS. In the year ended 31 December 2016, the Group’s Styrene Plastics Segment generated sales revenues totaling PLN 2,111 million and EBITDA of PLN 226 million.
Main products and applications
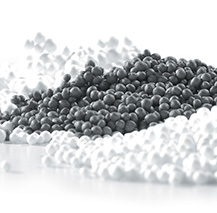
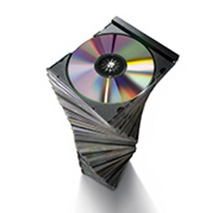
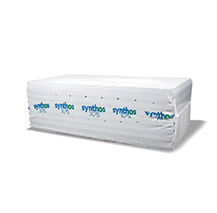
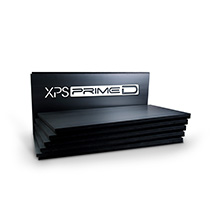
EPS is a polymer compound used as feedstock in the production of styrofoam. EPS may contain additives to enhance processing or equip the resulting foam with specific application properties, such as flame retarding agents, lower heat transfer, lower water absorption, external lubes facilitating processing, colorants etc. EPS produced by the Group is sold under the InVento® and InSphere® trademarks.
- Invento® is a self-extinguishing expandable polystyrene with a lowered heat transfer ratio and lowered contents of blowing This material is formed from spherical polystyrene particles. It contains a substance to diminish the flammability of foam and a hydrocarbon foaming agent. During production, the surface of these goods is treated against adhesion and the buildup of static electricity. InVento® 0814FR is intended mainly for producing thermal insulation blocks used to insulate buildings.
- InSphere® types 0513F, 0814F and 1020F are self-extinguishing expandable polystyrenes with a lowered heat transfer ratio. InSphere® type 0513FR-P is a self- extinguishing expandable polystyrene with lowered water absorption and lowered contents of hydrocarbon blowing agent. The material, made up from spherical polystyrene particles, contains a substance that lowers the flammability of foam and a hydrocarbon blowing agent. During production, the material’s surface is treated against adhesion and the buildup of static electricity. InSphere® type 0513F is used mainly to produce packaging for shipping glass and electric goods, building bricks, floor and shaped parts and other thermal insulation InSphere® type 0814F is used mainly to produce thermal insulation blocks and packaging InSphere® types 1020F and 1640F are used mainly to produce thermal insulation blocks. InSphere® type 0513FR-P is used mainly to produce perimetric and skirting boards of packaging for shipping glass and electric goods, building bricks, floor and roof shaped parts and other thermal insulation articles.
The Group also manufactures GPPS and HIPS products:
- SYNTHOS PS GP 137, 152, 535, 154, 525, 171, 585C, 174 and 545 are general purpose polystyrene resins (GPPS) produced to high specifications as regards optical properties, with glossy polish and increased heat resistance. This is a thermoplastic material intended for injection molding, extrusion, thermoforming and blowing extrusion. SYNTHOS PS GP 585A is a general purpose polystyrene resin (GPPS) with excellent optical properties, glossy polish, considerable resistance to high temperatures and mechanical durability. This is a thermoplastic material intended for extrusion, thermoforming and blowing extrusion. SYNTHOS PS GP 585X is a general purpose polystyrene resin (GPPS) that meets stringent requirements of considerable heat resistance and good reological properties. This is a thermoplastic material intended for extrusion, thermoforming and blowing extrusion.
- SYNTHOS PS HI 336M is a high impact polystyrene (HIPS) with easy flow, which ensures simple processing. This is a thermoplastic material intended for injection molding. SYNTHOS PS HI 552M is a general purpose high impact polystyrene (HIPS) with balanced reological, mechanical and thermal This is a thermoplastic material intended for injection molding and extrusion. SYNTHOS PS HI 562E and 945E are types of high impact polystyrene with properties suitable for extrusion and thermoforming. SYNTHOS PS HI 662E is a type of high impact polystyrene with matte finish, whose properties allow extrusion and thermoforming.
The Group manufacturers products from extruded polystyrene (XPS):
- Synthos XPS PRIME and Synthos XPS PRIME S are environmentally-friendly insulation products with a formula based on the Synthos XPS white
Customers
In the Styrene Plastics Segment, the Group focuses its activities mainly on servicing the construction industry and manufacturers of packaging from EPS and XPS. Its main customers for EPS products include Arbet (Koszalin), GPS (Poland), Termo Organika (Kraków), Austrotherm (Oświęcim), Bachl (Germany), Lippstaedter (Germany), Saint-Gobain (Germany). GPPS and HIPS products are sold mainly to the packaging industry, primarily to operators in the food sector. Main customers for this product group include Krakchemia (Kraków) and Huhtamaki Foodservice Group (Skierniewice) in Poland, Coveris Group (France), Polycasa (Belgium), Greiner (Austria), DFI (Italy). The Group sells XPS boards using two channels: wholesalers of construction materials and EPS processors that buy raw materials to produce EPS boards and also resell finished XPS insulation boards. Main customers for this product group include Termo Organika (Kraków), Saint-Gobain (Czech Republic), Styroprofile/Styrotrade (Czech Republic), SIG (Kraków).
Raw materials and sources of energy
The Group produces styrene from ethylene and benzene and uses it to manufacture the Group’s own derivatives, i.e., polystyrene, expandable polystyrene (EPS) and synthetic rubber. Extruded polystyrene (XPS) is produced on the basis of own raw materials, such as GPPS. The Group also purchases a certain volume of styrene on the market. As a result of large purchases, the Group is able to negotiate favorable formula-based prices.
Competitors
In 2016, in connection with the acquisition of the EPS business from INEOS, the Group became the largest manufacturer of EPS in Europe, and the largest manufacturer of XPS in Central and Eastern Europe.
The main competitors of the Group are INEOS, BASF and SUNPOR. INEOS and BASF are the world’s largest chemical concerns in terms of profits and Europe’s largest EPS producers, focusing on producing goods with excellent insulation properties. Both companies are vertically integrated and have a large product portfolio.
Highlights
The Group’s Dispersions, Adhesives and Latexes Segment produces acrylic dispersions, styrene and acrylic dispersions and vinyl dispersions; wood and paper adhesives, and two different types of synthetic latex: concentrated styrene butadiene and styrene butadiene carboxylic latex. The main application of dispersions is the production of high quality paints, acrylic plasters, primers, leveling compounds and many other chemicals used in the construction industry. Polyvinyl acetate dispersions are used in the manufacture of wood adhesives and in the paper, textile and construction industries. Adhesives are used mainly in the wood, furniture and paper industries. Latexes are used mainly to produce elastic latex foam and latex mattresses, gelled or non-gelled foam carpet backings, adhesive floor coverings and other carpet backing, to impregnate fabrics and to produce bitumen emulsions. In the year ended 31 December 2016, the Dispersions, Adhesives and Latexes Segment generated sales revenues totaling PLN 195 million and EBITDA of PLN 29 million.
Main products and applications
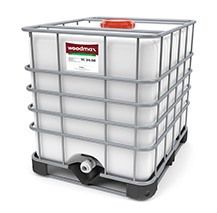
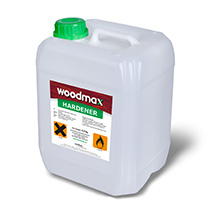
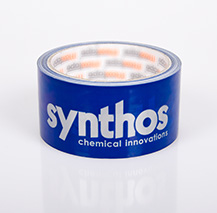
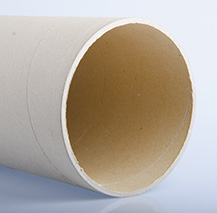
The current portfolio of the Dispersions, Adhesives and Latexes Segment includes products registered under the following trademarks: Osakryl®, Synexil®, Woodmax®, Papermax®.
- Osakryl® is a registered trademark for a range of water-based acrylic, styrene-acrylic and vinyl-acrylic copolymer dispersions obtained by emulsion polymerization. These dispersions act as a binding agent in chemicals used in the construction
- Synexil® is a registered trademark for a range of vinyl, acrylic, styrene-acrylic and vinyl-acrylic dispersions obtained by emulsion polymerization. These dispersions act as a binding agent in chemicals used in the construction industry and adhesives used in a variety of applications (mainly wood, wood-based materials, paper, cardboard, etc.).
- Woodmax® is a registered trademark for ready-made dispersion adhesives for use in the woodworking and furniture
- Papermax® is a registered trademark for ready-made dispersion adhesives for use in the paper and packaging
- Concentrated styrene butadiene latexes and carboxylated styrene butadiene latexes are the main raw material used in the production of foam products and an adhesive agent in bituminous/polymer
Customers
The main customers for dispersions are the leading manufacturers of liquid chemicals for the construction industry, including Śnieżka, Kabe, PPG and Atlas. The main export markets include Ukraine, Belarus, Czech Republic, Greece, Italy, Spain, Romania and the Baltic countries.
Woodmax® adhesives are sold primarily to manufacturers of furniture (predominantly IKEA) and wood joinery (Stolbud, Porta, DRE). Papermax® adhesives are intended for the paper industry and sold to manufacturers of packaging, tubes, corners, cardboard pallets and other paper articles.
Latexes are sold mainly to customers that manufacture floor coverings and carpets, foam products (latex sponges and mattresses) and bitumen emulsions for the construction industry. The main customers of the Group are Artilat (Belgium), the Beaulieu Group (Belgium) and Brintons Agnella (Poland).
Raw materials and energy
The main monomers used to produce dispersions, adhesives and latexes are vinyl acetate, acrylate esters, styrene, butadiene and others. The Group purchases these raw materials under both long-term and short-term agreements.
Competitors
The Group’s leading competitors in this segment are large international chemical concerns, such as BASF, DOW, EOC, Synthomer, Henkel and Jowat with large and diversified product portfolios.
Highlights
The line of business of Synthos AGRO is to produce and sell plant protection means, seed dressing agents, biocidal products and leaf fertilizers.
The plant protection products segment accounts for 63% of Synthos Agro’s revenues. Its product range consists of 18 products with fungicidal products for orchard plants forming the most extensive product group. Synthos Agro holds a 16% market share in this product group. In the year ended 31 December 2016, the Agro Segment generated sales revenues totaling PLN 81 million and EBITDA of PLN 3 million.
Main products and applications:
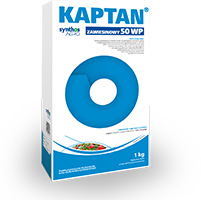
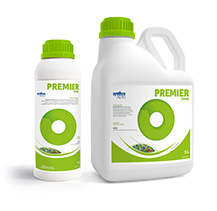
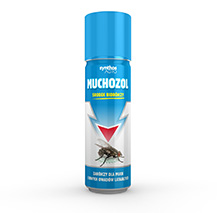
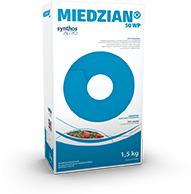
- Fungicides This group consists of products for preventive application prior to the appearance of fungi diseases in orchard plant crops, especially against apple scab, the fiercest disease threatening healthy yields:
- Miedzian 50 WP, Miedzian Extra 350 SC - market leaders in the product group based on copper compounds
- Kaptan Zawiesinowy 50 WP
- Kaptan Plus 71.5 WP
- Sadoplon 75 WP - Seed dressings Seed dressing agents are generally applied fungicides to dress seeds before sowing. Dressing is the first protective measure and at the same time the main and least expensive method of combating pathogens in the soil that are transmitted with seeds. Dressing affords protection to seeds when they are sprouting while also ensuring plant health in the earliest stages of their growth and development. The following represent this group:
- Zaprawa Nasienna T 75 /WS [Seed Dressing Agent T 75 DS./WS] - to dress wheat, rapeseed and vegetables to the greatest extent available on the market
- Funaben Plus 02 WS- to dress wheat and barley seeds - Herbicides This group includes herbicides intended for use in agricultural and horticultural crops:
- Orkan 350 SL – for use against horsetail and other deep-rooted weeds in orchards
- Premier range: Premier 350 SL, Premier 500 SL, Premier 750 SL and Premier D 750 SL – for use by farmers in weed control of winter and spring - Biocidal products This category of products targets the mass market and are dedicated to private users. This category has an extensive range of products, chiefly aerosols to apply against bothersome insects such as flies, wasps, locusts, ants and mosquitoes, and other forms, such as poisons and granules for rodent control. Muchozol and Mrówkozol are the best known brands.
Customers
The buyers of Synthos Agro’s products are entities operating on the market of professional purchasers and private (non-professional) users who purchase these products to protect their crops. Product distribution is handled by a nationwide network of wholesalers offering agrochemical and horticultural products with whom Synthos Agro has signed long-term distribution agreements. The Company’s installations and extensive capital expenditure efforts aimed at the construction of a new state-of-the-art formulation and packaging center make Synthos Agro a solid and reliable partner in developing a range of products for a number of domestic and foreign customers.
CompetitionSynthos Agro operates in a highly competitive market environment. The major competitors operating on the market are well-known global concerns with an abundant product range such as BASF, Bayer, DuPont, Syngenta, Adama, Arysta.
The Group pursues operational activities related to the generation and distribution of thermal energy, the generation of electricity and the sale and distribution of electricity. The Group’s combined heat and power plants are located in the industrial facilities in Oświęcim (Poland) and Kralupy (Czech Republic). At Oświęcim, the main fuel used by the Group is black coal from local mines. In addition, the Group derives some of its energy from “coal bed methane,” that is fuel gas extracted in some underground mines for the purpose of subsequent coal extraction. In the Czech Republic, the Group’s main energy sources are natural gas and, to a certain extent, fuel oil.
Moreover, Other Operations include all other lines of business in which the Group is involved to a limited and auxiliary extent and which are not assigned to any of the above segments, including sales and distribution of auxiliary utilities, laboratory services and lease of industrial buildings and warehouse facilities. Other Operations include also all costs not allocated to the above segments.
For the year ended 31 December 2016, the area of Other Operations (including the Utilities Segment referred to in the consolidated financial statements) generated sales revenues of PLN 222 million and EBITDA of PLN 41 million.
The Group sells synthetic rubber predominantly to global producers of tires such as Michelin, Pirelli, Goodyear, Bridgestone and Continental.
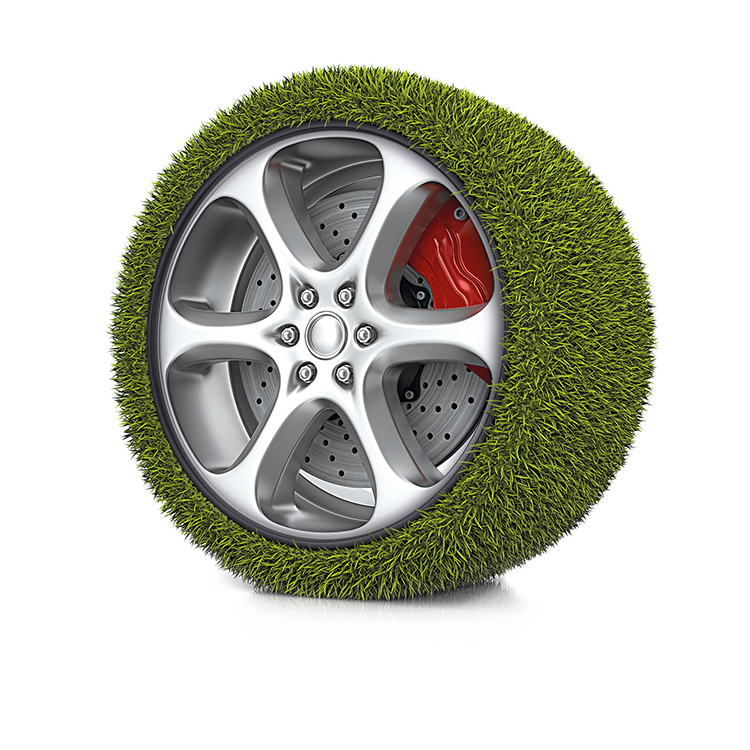
The Group sells synthetic rubber predominantly to global producers of tires such as Michelin, Pirelli, Goodyear, Bridgestone and Continental, many of which are well known market leaders. The Group’s production facilities are strategically located near these key customers in Central Europe, with easy access to tire plants as well as to areas of growing demand.
The Group’s marketing team consists of three persons cooperating with Category Managers paced directly in the segments. The marketing strategy is initiated by the Group’s global marketing team, with specific market activities further developed and implemented by each segment. In particular, the Group’s global marketing team is responsible for general market analyses, advertisement and promotion, while marketing teams in particular segments tailor and implement this marketing strategy within their domains by conducting market analyses, monitoring customer satisfaction, analyzing competition and promoting the Group’s products in new markets outside Europe.
The Group’s main raw materials are butadiene, C4 fraction, ethylene, benzene, ethylbenzene and styrene, of which butadiene and styrene are the most significant for its business.
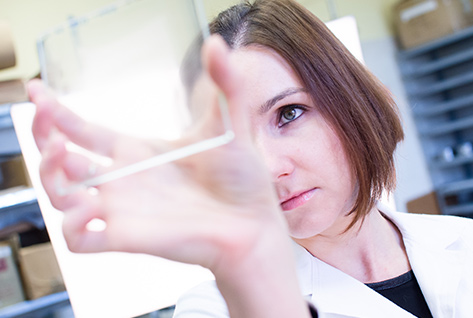
The Group’s main raw materials are butadiene, C4 fraction, ethylene, benzene, ethylbenzene and styrene, of which butadiene and styrene are the most significant for its business. In the year ended 31 December 2016, butadiene accounted for 20.7%, while the styrene accounted for 34,4% of the Group’s total expenses on raw materials. The Group buys butadiene or manufactures it on its own from C4 fraction. Another important raw material for its business is styrene, which the Group produces from ethylene and benzene (through ethylbenzene) at its Czech plant and buys on the market. In Poland, the Group produces styrene from ethylbenzene supplied from its plant in the Czech Republic. In the year ended 31 December 2016, the Group’s self-sufficiency in key inputs was as follows: approximately 47% for butadiene, 39% for styrene, 81% for ethylbenzene, and 112% for heat and 166% for electricity.
The Group’s main suppliers include European petrochemical producers such as PKN Orlen (combined together with Unipetrol to form a single group), Sabic, MOL and OMV, that deliver raw materials to the Group’s production facilities in the Czech Republic and Poland. The Group’s regional production facilities are also linked through pipelines with some of its suppliers, including a pipeline with Unipetrol through which the Group obtains C4 fraction, ethylene and benzene for its production facility in the Czech Republic. Moreover, in the year ended 31 December 2016, Butadien Kralupy a.s., the Group’s joint venture established in cooperation with Unipetrol, provided the Group with approximately 47% of the Group’s annual demand for butadiene.
From August 2015 to October 2016, the Group’s activities were impacted by a failure of the cracker at the Unipetrol plant in Litvinov and the subsequent announcement of force majeure circumstances. Restricted supplies of C4 fraction, ethylene, benzene and butadiene had an adverse impact on the Group’s cost structure and financial results.
The following is a detailed list of contractual arrangements under which the Group sources its main raw materials:
- Purchases of butadiene, which is used for the production of synthetic rubber and latex, are carried out primarily under long-term contracts with suppliers with stable market positions. These long-term agreements are from three to ten years or are concluded for an indefinite Some of them include renewal clauses. Raw material purchases are based on pricing formulas related to market prices of butadiene. In addition to securing raw material supplies through long-term agreements, the Group purchases supplementary amounts of butadiene under short-term contracts.
- Vinyl acetate monomer, which is used for the manufacture of vinyl and vinyl-acrylic dispersions, is purchased under annual as well as short-term agreements concluded with suppliers offering the best commercial terms at a given
- Ethylene and benzene used for ethylbenzene production are purchased primarily under long-term agreements concluded with Unipetrol, valid until the end of 2017, with prices based on pricing formulas linked to market prices of ethylene and benzene. Simultaneously, small amounts of benzene have been purchased under short-term
- Purchases of C4 fraction used in the production of butadiene are made under long-term agreements, with prices based on pricing formulas linked to market prices of
- Auxiliary raw materials for all types of chemical production, due to their relatively high level of availability, have been purchased mainly under short-term agreements in order to obtain more favorable commercial
The Group chooses its raw material suppliers from among the most reliable producers and suppliers that are able to offer the most competitive terms. All suppliers of materials to the Group are subject to constant reviews and assessments.
Key sources of energy
The Group’s combined heat and power plants are located in the industrial facilities in Oświęcim (Poland) and Kralupy (Czech Republic). At Oświęcim, the main fuel used by the Group is black coal from local mines. In addition, the Group derives some of its energy from mine gas. In the Czech Republic, the Group’s main energy sources are natural gas and, to a certain extent, fuel oil. In the year ended 31 December 2016, the costs of hard coal, mine gas and natural gas used for heating accounted for 5% of the Group’s cost of sales of products and materials.
The Group has production facilities in Poland, the Czech Republic, France and The Netherlands to produce synthetic rubber, styrene products, dispersions and adhesives and plant protection products.
The following table provides an overview of the Group’s production facilities and the main products manufactured there as at 31 December 2016:
Country | Segment | Main products | Production capacity kt/y |
---|---|---|---|
Poland | Synthetic rubber - EPS XPS* PS Dispersions and adhesives Latexes | ESBR, NBR. HSR SSBR EPS XPS HIPS, GPPS Dispersions, adhesives Latex | 185 90 105 165 50 58 16 |
Czech Republic | Synthetic rubber EPS XPS* PS | ESBR EPS XPS HIPS, GPPS | 110 105 165 80 |
France Wingles France Ribecourt | EPS ESP | EPS ESP | 100 75 |
The Netherlands Breda | EPS | EPS | 145 |
In addition, the Group owns 49% in a joint venture established with Unipetrol, which in the year ended 31 December 2016 provided the Group with 47% of its annual demand for butadiene, the key raw material for the Group’s synthetic rubber production at its production facility in the Czech Republic.
The Group considers research and development activities an important tool for competing effectively and commits significant resources to such activities.
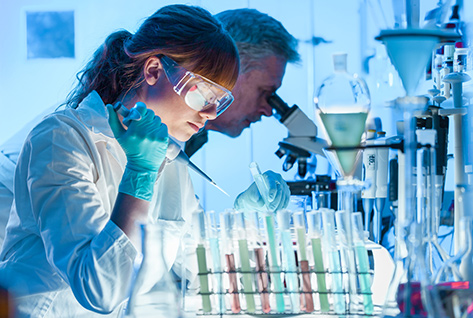
The Group’s research and development division is located in Poland and the Netherlands, consists of 96 people and focuses mainly on product development in three strategic areas: synthetic rubbers, expandable polystyrene (insulation materials), and dispersions and adhesives. Moreover, research work is conducted on plant protection products and liposomes. The Group owns key intellectual property and know-how in these areas. The Group’s R&D division has many ongoing research partnerships with external institutes, ranging from outsourcing of non-core activities to joint research and development efforts. The Group currently maintains a domestic and international relationship network with reputable scientific centers, e.g. the University of New Hampshire (USA), Global Bioenergies (France), the Fraunhofer Polymer Pilot Plant Center (Germany), VSCHT (Czech Republic), the Adam Mickiewicz University Foundation in Poznań, the Institute of Industrial Chemistry and the Institute of Organic Industry in Warsaw. This allows the Group to develop innovative products in a timely and cost-effective manner, taking into account the preferences and specifications of its customers.
Last year, work on several dozen projects continued. Some of the recently introduced new products include: Woodmax OC 14.50, a one-component adhesive of the highest water resistance class; Synexil AF 33, a self-crosslinking acrylic dispersion for wood of a very high hardness and scratch resistance; Premier 300 SL and D 750 SL, herbicides in concentrated form for the preparation of an aqueous solution, to be applied on leaves, intended to control annual dicotyledonous weeds in winter and spring cereals.
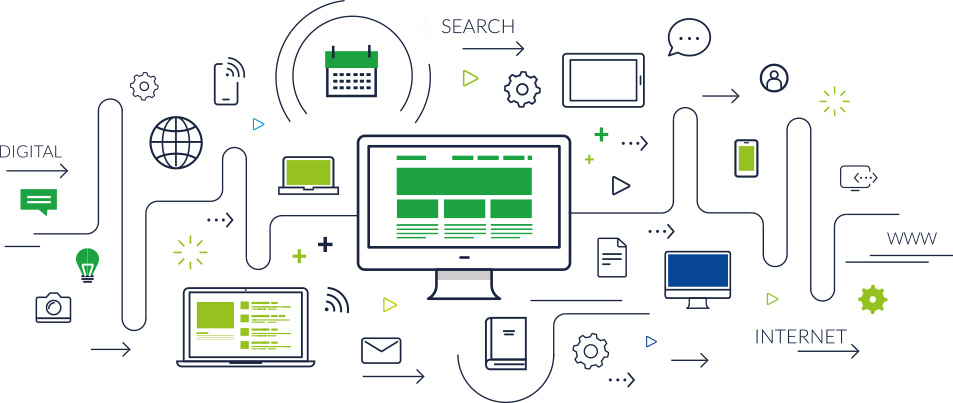
The Group uses several business support applications. An enterprise resource planning (ERP) platform supports most of the Group’s basic management and business processes, and assists in the forecasting and budgeting process, in terms of sales, production, purchasing and quality as well as fixed and variable costs and cash flows. Budgeted activities are recorded operationally in different operational modules, which allow the Group to oversee processes and at the same time monitor and block undesirable actions (such as exceeding customer credit limits, late payments or shortages/surplus in inventory levels).
In addition to the Group’s ERP system, the Group uses tools for analyzing and reporting data, such as the Business Intelligence system. Additionally, advanced warehouse management, registration of manufactured goods and completion of customer shipments are carried out using a warehouse management system. The Group has not had any significant IT problems in the past.
The Group has developed and maintains an extensive portfolio of registered patents and trademarks. Proprietary protection of the Group’s processes, apparatuses, and other technology and inventions is of essential importance to its business. In addition to the Group’s patents, patent applications, trademarks and know-how, the Group is party to certain licensing arrangements and other agreements authorizing the Group to use trade secrets, know-how and related technology or operate within the scope of certain patents owned by other entities. Because of the breadth and nature of the Group’s intellectual property rights and the Group’s business, the Group is not wholly dependent on any single intellectual property right.
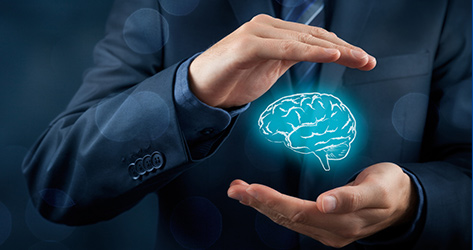
The Group is not aware of any threatened, proposed or actual proceedings that have been or will be brought against the Group for infringement of third party rights or any infringement of the Group’s rights by third parties that if successfully prosecuted would have a material adverse effect upon the Group’s business, results of operations, financial condition or prospects.
The Group anticipates that environmental spending in the near future will be directed to eco- innovative solutions.
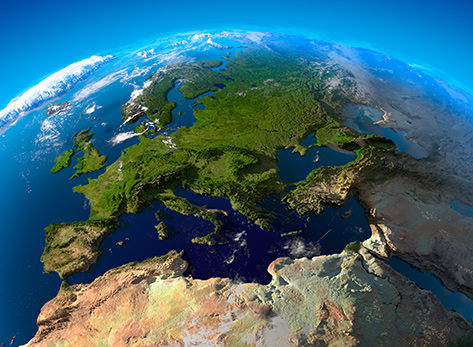
Environmental Performance
Like other chemical manufacturers, the Group’s operations are subject to a broad array of environmental laws and regulations. The Group’s manufacturing processes use numerous chemicals, gases and other hazardous substances. The Group strives to minimize the impact of its operations on the environment through an efficient use of raw materials and energy, management of waste and the development and application of solutions aimed at reducing air, water and soil emissions and improving the security of the Group’s technological installations.
The Group is also subject to increasingly stringent environmental, health and safety (EHS) laws and regulations, including those governing air emissions; water supply, water use and discharge of sewage into water; construction and operation of facilities; use, management, storage and disposal of waste and other hazardous materials; health and safety of the Group’s employees; investigation and restoration of contaminated soil; the impact of the Group’s products on health; and general occupational health and safety issues. The Group is required to obtain and periodically renew permits or licenses for industrial operations that result in discharge into the soil, air or water as well as in the use and handling of waste and other hazardous materials. Such permits and licenses establish limitations and standards with respect to the Group’s operations that require compliance. The Group complies with the highest standards of care and employs suitable numbers of personnel to ensure adequate management of waste. The Group’s facilities are regularly audited and inspected by governmental bodies in both Poland and the Czech Republic.
Apart from other EHS laws and regulations, the Group expects that its business will over the next few years be affected by new legal requirements under the IED, the EU ETS, the environmental liability directive (ELD) and the REACH Regulation, all of which impose significant obligations on the Group’s business with respect to the testing, evaluation, assessment and registration of basic chemicals and chemical intermediates. The IED and EU ETS directives aim at reducing the emission of pollutants and greenhouse gases into the air.
In particular, the IED has introduced, effective from 1 January 2016, tighter emissions standards for SO2, NOx and dust from existing heat and power plants such as the Group’s.
The Group anticipates that environmental spending in the near future will be directed to eco- innovative solutions. The Group estimates that it will spend approximately PLN 20 million in 2017.
Occupational health and safetyThe Group’s main environmental initiative relates to its energy sources, such as constructing an installation for desulfurization and NOx removal. In addition, the Group’s new coal boilers in Poland and the Czech Republic will comply with all European and Polish environmental requirements. Moreover, the Group is committed to manufacturing safe products and achieving an incident-free workplace. To protect its employees, the Group has established health and safety policies, programs and processes at all its sites.
Safety of Group employees is one of its priorities. The Group constantly monitors work conditions, making improvements as necessary. The Group’s employees play a key role in this process by providing suggestions for improvement during risk assessments, which are reported under the Group’s special KAIZEN management system. During the last five years, the Group has not noted any fatal accidents or accidents causing serious injury.
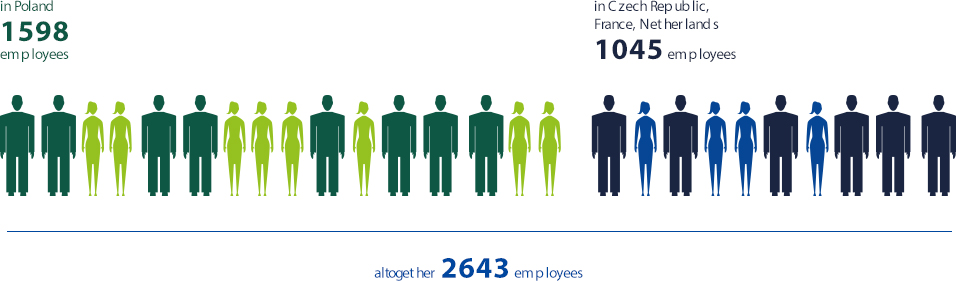
As at 31 December 2016, the Group employed 2,643 staff, mainly in Poland (1,598 persons). The other staff were employed in the Czech Republic, France and the Netherlands.
As a result of the technical nature of the Group’s business, the Group maintains a highly qualified and skilled workforce and emphasizes the importance of regular training and development of employees through participation in training programs. The Group also promotes employee development using a system of annual and quarterly bonuses.
The Group believes that its labor relations are good. The Group’s terms of employment are subject to negotiations with trade unions each year. The negotiations usually start in the third quarter of the year and conclude with the signing of an agreement which outlines new terms forming part of the Group’s internal labor regulations. In Poland, the Group is also subject to certain Polish wage regulations, and employees of all companies are subject to comparable remuneration terms set forth in the Remuneration Regulations. In the Czech Republic, the Netherlands and France, the Group operates under collective bargaining agreements. The Group generally aims to systemize and standardize its wages, while preserving certain minor distinctions. The percentage of employee unionization is 53% in Poland and 29% in the Czech Republic. In the last five years, the Group has not been involved in any disputes with trade unions.
There are no employee share schemes in the Group.
The Group believes that the types and amounts of insurance coverage the Group currently maintains are in line with customary practices in its segment of the chemicals industry and sufficient for the conduct of the Group’s business. More specifically, the Group has insurance policies with a number of international and local insurance companies covering certain operating risks, including damage of specific property, operational and product liability, cargo in transit insurance (for selected companies), rolling stock and vehicles insurance (in selected locations) and receivables insurance (for selected receivables).
The Group is involved in a number of court proceedings in connection with the ordinary course of its business. These include actions initiated by regulatory authorities, tax authorities, suppliers and customers, claims advanced by employees, contractual disputes, claims for personal injury or property damage that may occur in connection with the Group’s services related to projects or construction sites, tax assessments issues, environmental claims and other matters. Many of the Group’s agreements contain provisions relating to alternative dispute resolution proceedings that allow to settle any contractual disputes. If the parties to the agreement are unable to reach an agreement, it may be necessary to initiate court proceedings to resolve the dispute.
Apart from the matters disclosed in this document, in 2016 the Group was not involved in any governmental, legal or arbitration proceedings (including any pending or threatened proceedings of which the Group is aware), which in the recent past have had, or in the future may have, a significant impact on the Group’s financial standing and profitability.